The injected melted material is then cooled in the mold until it returns to a solid state, enabling the molded part to be extracted from the mold. Injection molding is a manufacturing technique that can be used to produce many different types of plastic products, such as toys, electronics, automotive parts and other consumer goods.
Injection machines are generally classified into single-cylinder, double-cylinder and four-cylinder according to the number of hydraulic cylinders that operate them. Injection machine manufacturers provide several models with a variety of features.
Clamping Stage: The two halves of the mold are securely closed by a hydraulically powered clamping unit before the material is injected into the cavity. The clamping pressure complements the applied injection pressure and is necessary to improve the compactness of the molded part as well as to control shrinkage, cooling and ejection.
Injection Speed: The screw of the injection unit rotates at a high rate to transfer the molten plastic into the mold cavities. The speed of the injection screw is determined by several factors, including the volume of the injected material and the size of the mold.
Runners: Channels integrated into the mold design carry the melted plastic from the sprue to all the cavities that require filling. Each runner contains an inlet that directs the flow of molten plastic, and at the end of each runner there is a gate that opens into the cavity.
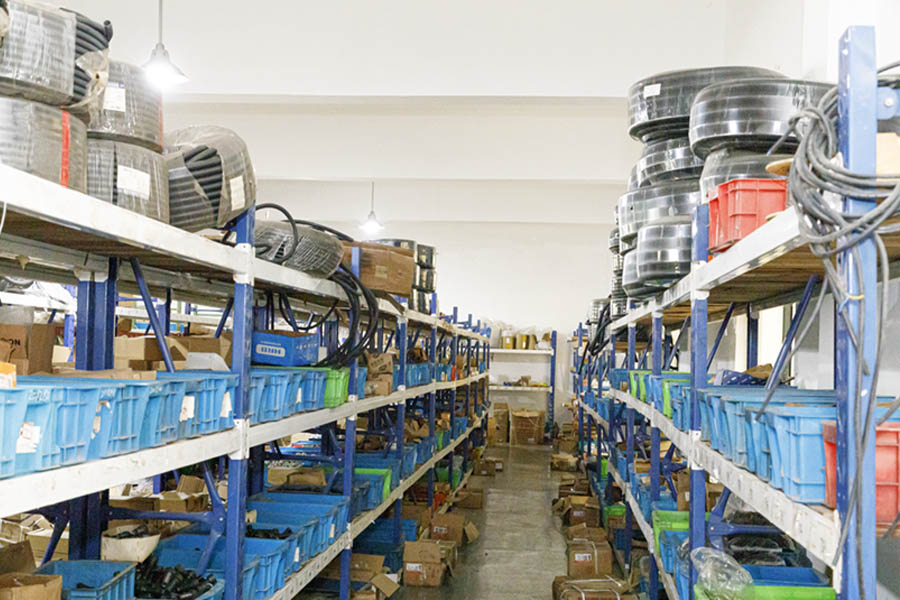