Although the injection molding process is a highly efficient one, there are still several issues that can cause damage to your parts. Fortunately, there are a number of things you can do to prevent defects and improve the quality of your production.
Problem #1: Sink Marks
If you notice sink marks on your parts, it means the molten plastic is not flowing evenly into the mold cavity. This can be caused by a variety of issues, including incorrect injection pressure, gate size, or mold venting.
Problem #2: Waves on the Surface
When a part cools quickly, it can cause waves to form on its surface. This can lead to chips, cracks, and other imperfections on your part.
Problem #3: Flow Lines
Flow lines are another common molding defect that can form a wavy pattern on your product’s surface. They are caused by a variety of factors, including low material temperature and a small gate size.
Fortunately, you can solve these problems easily with a few minor adjustments to your process. You can increase your injection speed, decrease your pressure, and maintain a certain mold temperature to ensure your part is filled and solidified before cooling. You can also round the corners of your mold to ensure that the plastic reaches the corners before it starts to cool. These simple adjustments can help you produce high-quality, finished products without a lot of flaws.
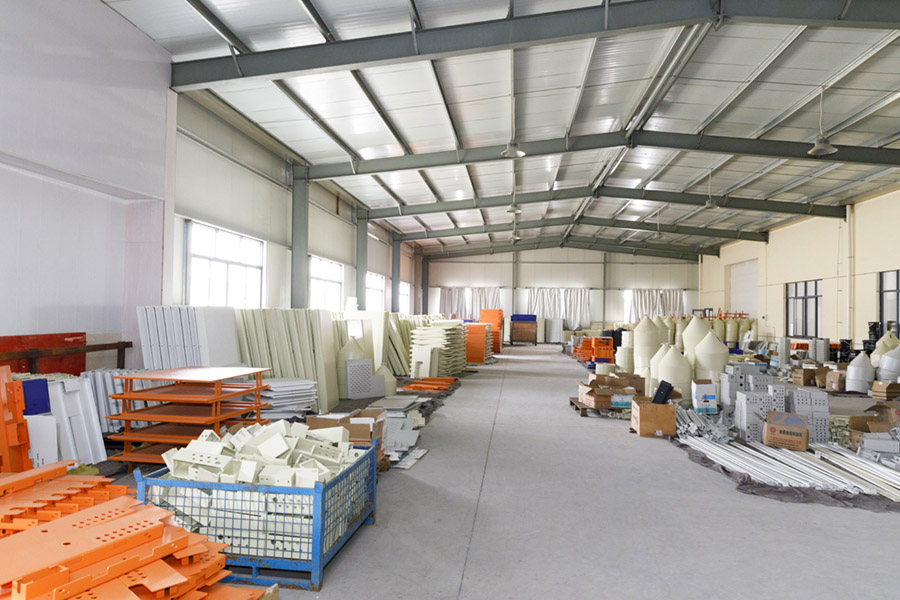