There are many different types of injection molding machines and each can be used for a wide range of applications. There are hydraulic, electric, and hybrid machines, each with its own unique set of features.
The most common injection system is the reciprocating screw, a mechanism that melts plastic in a barrel and then transfers it to the mold through a plunger. This injection system is typically found in modern, automated injection molding machines.
Clamping Pressure
The clamping pressure required to hold the two halves of the mold in position is a critical factor in ensuring the injection molding process is successful. Insufficient clamping pressure can result in leaks, flashes and the development of part defects. Excessive clamping pressure can lead to a number of equipment failures, including cracked platens, hydraulic cylinders, and mold vents.
Material Options
There are many different kinds of materials that can be molded into plastic parts through the injection molding process. The most common are thermoplastic polymers, which can be repeatedly melted and re-molded in the mold without losing their physical properties.
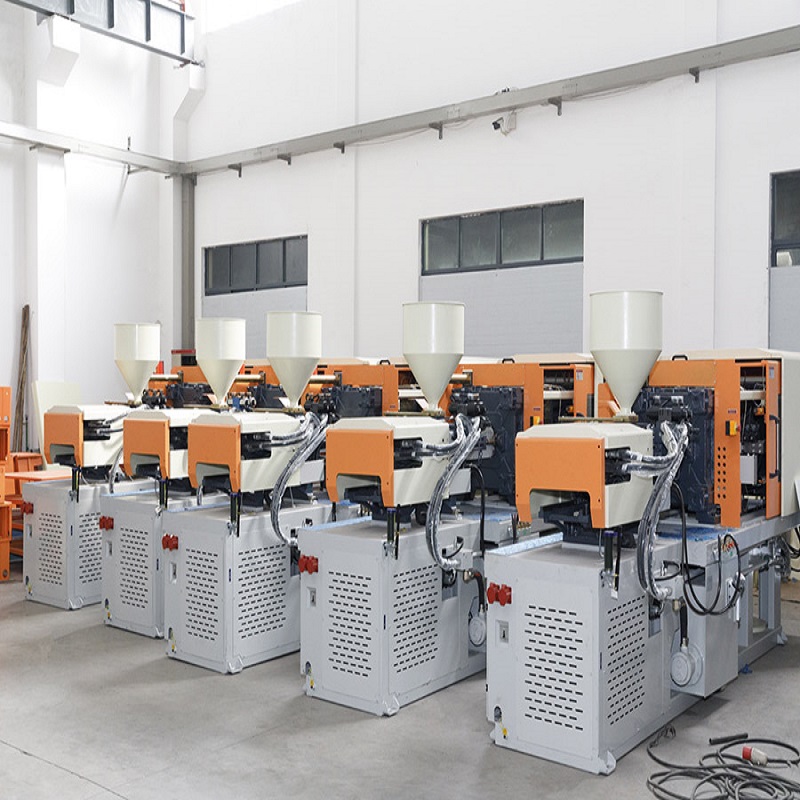