The first step in the process is to feed a hopper with a pre-measured amount of raw plastic and the appropriate additives. Then, a heating unit adds heat to the raw material to melt it and a ram injector or reciprocating screw moves forward to inject it into the barrel of the mold.
After the injection, the screw and barrel heaters are turned off. The plastic has now cooled, and it can be removed from the mold by an ejector system that opens the mold to a solid part.
Injection Molding: Minimizing Tooling Costs
Aside from the material, the tooling costs associated with Injection Molding are one of the biggest factors that determine overall production costs. This includes the design of the part itself, and the specialized features like threaded inserts that allow assembly and disassembly.
Injection molded parts are often manufactured with tolerances that are as small as 10 micro meters (or a tenth of a human hair). The best way to minimize the cost of your project is to optimize your design for precision and cost efficiency.
Another way to decrease your cost is to reduce the maximum wall thickness of your product, as this greatly speeds up the injection molding cycle and saves you money. Moreover, reducing wall thickness can also improve the quality of your product.
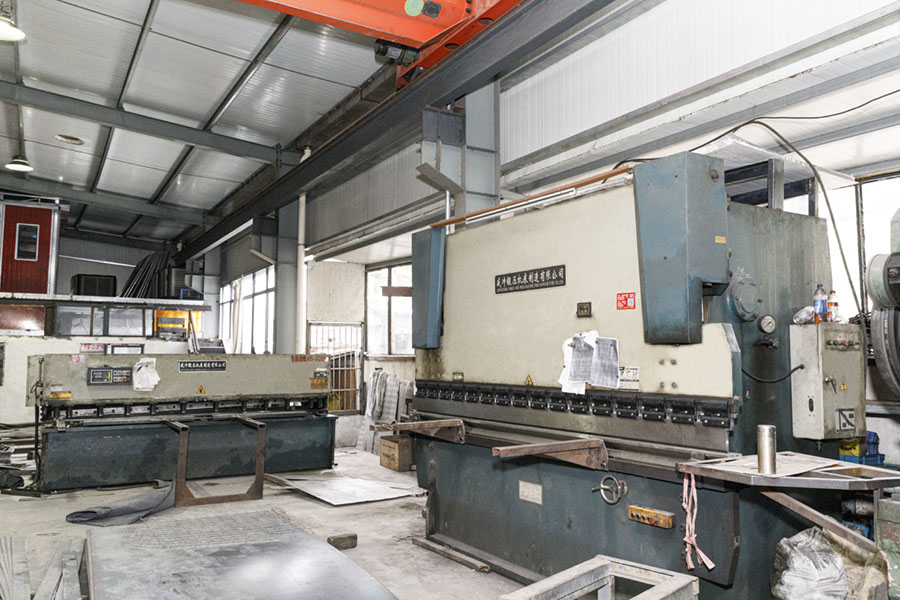