Injection molding machines come in a variety of sizes and designs, but all share the same basic components. These include a hopper, barrel, and reciprocating screw.
Regardless of the type of injection molding machine you choose, you will need to make sure that it is capable of producing the part you want. This means that you will need to consider what the material is and how large of a volume you need the machine to be able to produce.
You will also need to consider the cost of the machine. If the machine is going to be used a lot, you may want to look for one that can reduce its operating costs.
Another consideration is the strength of the parts that you are going to produce. You will need to ensure that the material you use is not too stiff, which will make the molded parts less durable.
Designing your Parts for Injection Molding:
When designing your product it is important to keep the wall thickness uniform throughout the part. This is essential for reducing production time and improving the quality of your molded parts. If the walls are not uniform, they can warp and cause defects. It is also possible to increase the strength of your part by adding ribs at key locations.
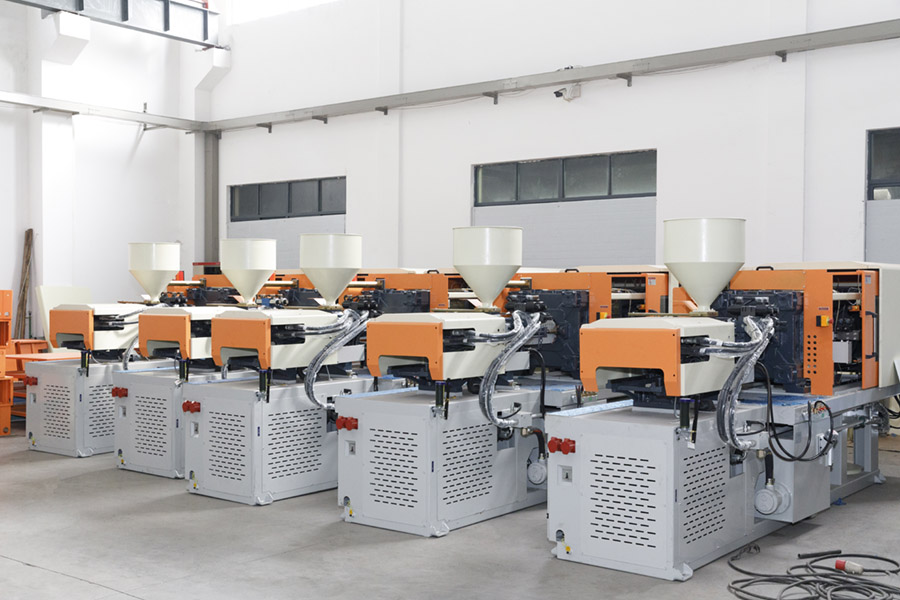