There are many types of injection molding machines and the best machine for your needs will depend on the type of product, the quantity required and how precise you want the finished part to be. It is important to find a manufacturer with expertise in a wide range of injection molding processes and the latest technology.
Types of Injection Molding Machine:
The injection molding machine consists of an injection unit and a clamping unit. The injection unit injects the melted resin into a mold cavity and the clamping unit holds the mold closed.
Screw and Barrel Heaters
The screw and barrel heaters in an injection molding machine add heat to the raw material to melt it before injection into a mold. They also remove heat after the mold "shot" to cool and harden the molded part.
Hot and Cold Runner Systems
The person designing the mold chooses whether the mold uses a cold runner system or a hot runner system to carry the plastic and fillers from the injection unit to the cavities. A cold runner system is simple, often using carved channels that the part will enter into after being ejected.
Toggle-type Injection Molding Machines
Toggle-type molding machines amplify the force of the injection process by adding a pivoting toggle to the two bars that connect to the platens. This amplifyr system allows for the production of smaller, more complex parts and lowers operating costs.
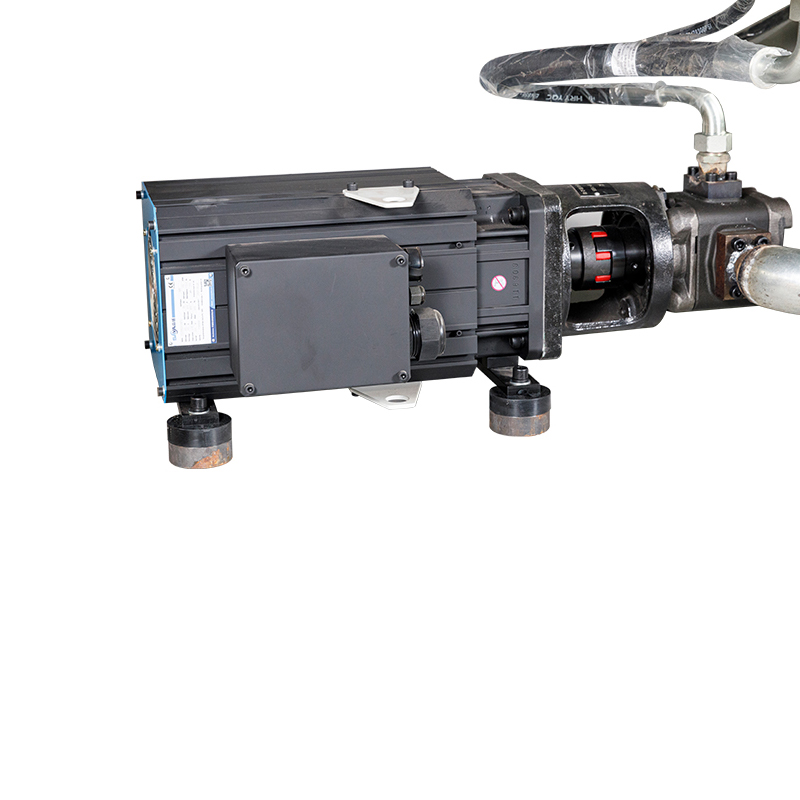